
Plant Maintenance and Upgrade
Plant Maintenance and Upgrade services
- BMS Design & Commissioning
- Read Our Latest Blog
Plant Replacement strategy: when and why?
- Age
- Maintainability / Serviceability.
- Efficiency & performance.
- Condition – Wear & Tear.
- Obsolescence and operational costs.
- Change in equipment or building use.
- Breakdown and frequency.
- Criticality and risk of failure.
Condition-based Report | Understand your building better.
Effective planning and budgeting is a critical aspect of property and facility management. To ensure efficient operations, we should plan, forecast, and establish conditions. Whether you are onboarding a new property or acquisition, creating an asset list and condition-based report is the first step that must not be overlooked. This report should provide detailed information on plant life expectancy and any other limitations that could affect the building performance. Extracting this information from a new building is relatively easy if you have a comprehensive Operations & Maintenance Manual (O&M). However, it can be more challenging to achieve in older buildings where historical data may not be readily available. Therefore, it becomes necessary to undertake an acquisition and condition-based survey.
Creating this report helps to identify every risk associated with the property’s condition, age, and serviceability from the outset. It ensures that any plans for improvement, plant replacement, or upgrades are factored into future budgets, allowing for smoother operations and better management of resources. By taking proactive measures to establish the property’s condition, you can mitigate any potential risks and avoid costly repairs in the long run.
MAINTENANCE
PLANT REPLACEMENT REVIEW
METERING
Underpinning any plant replacement strategy is the effective use of sub-metering. Developing sub-metering strategies for all utilities and equipment at end use provides further insight, intelligence and monitoring capability to not only identify waste but also as a tool to monitor performance and effectiveness.
Energy & Technical Services Ltd has many years of experience in preparing:
- Plant replacement programmes.
- Capital expenditure forecasts.
- Maintenance monitoring and effectiveness.
- Lifecycle analysis and feasibility.
- Energy saving initiatives & evaluation.
- Energy auditing and surveying.
- Performance specifications for plant replacement.
Project management and delivery of plant replacement strategies and initiatives.
PLANT LIFECYCLE
The operating characteristics of any plant, system or equipment throughout its lifecycle tend to have higher failure rates in the ‘bedding’ in the process when it becomes operational and higher failure rates towards the end of its life expectancy. Between those two points, there is a stable operating base. This is often illustrated in the form of the ‘bathtub’ diagram depicted below:
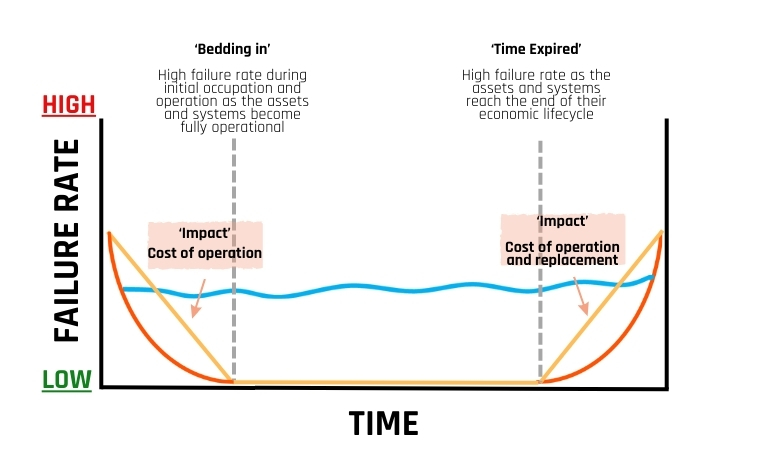
‘Bedding in’ failures when the system is newly commissioned is standard. The failure rate will increase towards the end of plant life expectancy, and eventually, it will become uneconomical to run the plant. For example, we can obtain plant life projections from manufacturers’ literature or the Chartered Institution of Building Services Engineers (CIBSE) Guide.
Age is also a factor in obsolescence; as the plant nears or exceeds its life expectancy, you are likely to find that spares for repair become increasingly complex to source, more expensive and ultimately, uneconomical to operate.
STRATEGIC PLANS & BUILDING USE
An appreciation of the strategic plans of a building must be understood. This extends to refurbishment, alteration and changes in use. Original base build HVAC systems and the plant can be significantly limited if a site use and application is changed but with little consideration of plant layout, capability and design. Poor environmental performance and internal comfort conditions are most likely to ensue, and the plant might become uneconomical to operate if there has not been any modification to the original base build systems.
TECHNOLOGY
Our Plant Replacement Strategy drives a sustainable and long-lasting building.
Our plant replacement strategy involves comprehensive condition-based reports that give you a better understanding of equipment and continuing maintenance that acknowledge you with complete control. We aim to promote a healthy and thriving ecosystem within and around the building, which supports business growth, improves air quality, reduces energy costs, and enhances the overall aesthetics and functionality of the space.
with 25 years of experience in plant maintenance services, energy & Technical Services has the magical touch!
Our game-changing solutions will whisk you towards long-term triumph.
The Reality of Energy Management for Building Occupants
The Power of Smart Building Technology
F-Gas Regulations: The Impact on Facilities Managers
THe benefits of Plant Maintenance and Upgrade
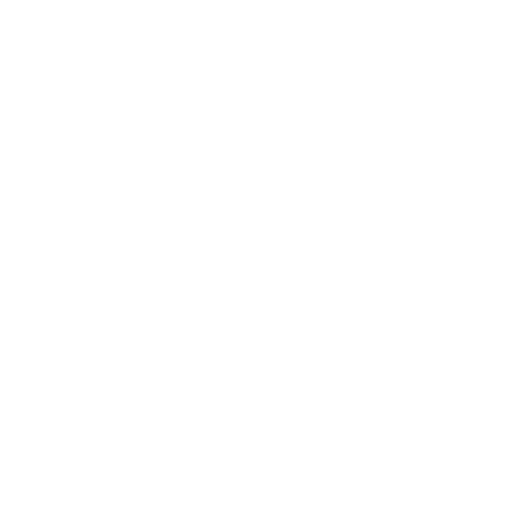
reduce energy costs
Give your gear a little TLC with regular maintenance and survey – it’ll live longer, and save you from costly repair bills down the road.
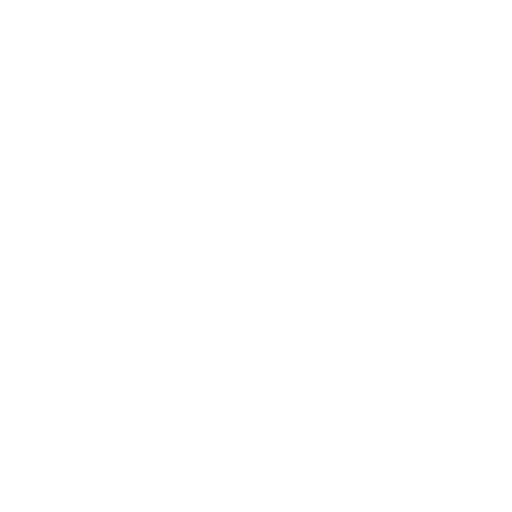
guaranteed air quality
With the improved plant performance,
carbon emissions can be controlled and
reduced following by energy waste reduction.
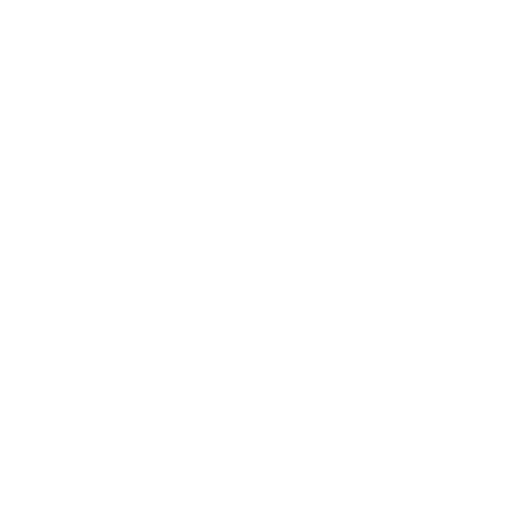
Centralised management
Keep your equipment in tip-top shape with regular maintenance to ensure efficient performance, ditch downtime, and rule productivity like a pro.