THIS ARTICLE AT A GLANCE
CONTACT ETS
If you have any questions or would like to discuss further what you should be doing, ETS is here and willing to help.
Call 0117 205 0542
Email enquiries@energy-ts.com
Submit a contact form
CHECK OUR SERVICES
Developing a Preventative Maintenance Plan – Top 10 Non-Conformance Issues
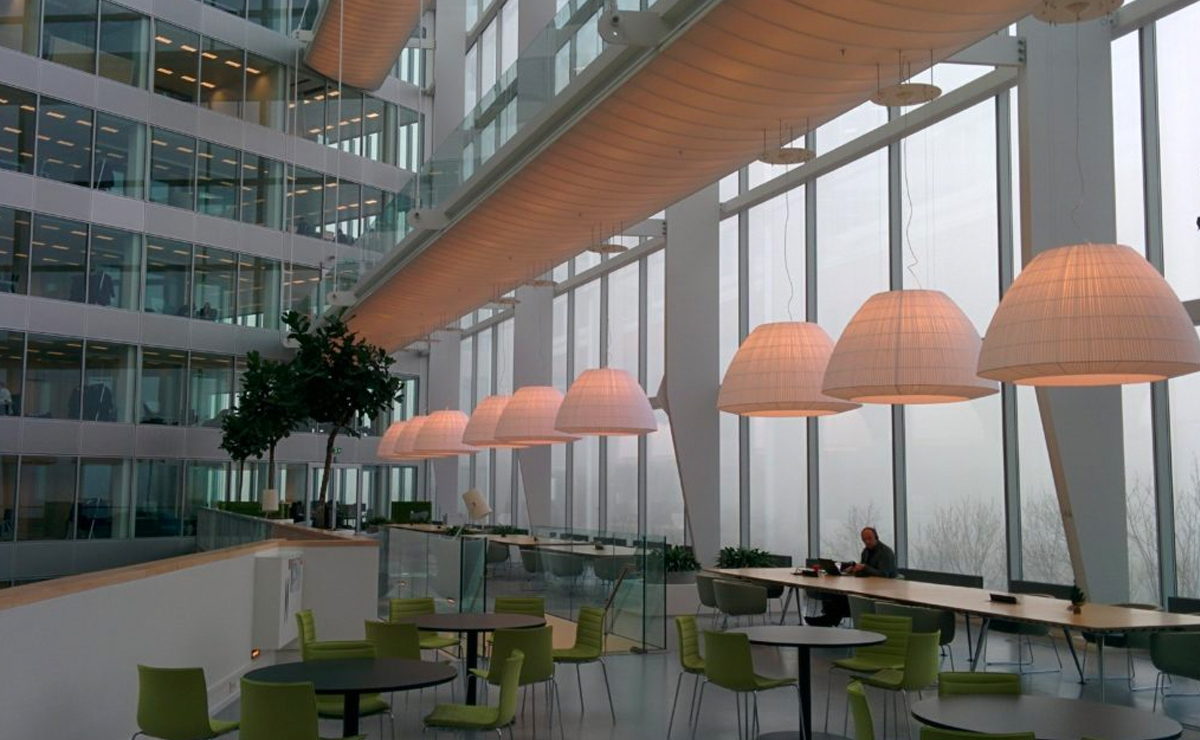
What is a PPM Audit?
Planned preventative maintenance (PPM) is designed to ensure that plant and equipment is regularly maintained in line with manufacturers recommendations. The purpose of PPM is to reduce reactive maintenance and prolong plant life expectancy.
PPM audits ensure that the incumbent contractors responsible for maintaining sites are carrying out their duties as per contract. A PPM Audit will also check that the maintenance provider is adhering to SFG20 standards, assuming this was an inclusion within the contract. In addition, a PPM audit will also review and comment on conformance items such as water hygiene, F Gas, electrical testing etc. which require completion in order to maintain legal compliance.
Our consultants carry out regular PPM Audits on behalf of our clients. Associate Director, Steve Shires discusses the top 10 non-conformance issues uncovered when conducting PPM audits.
F Gas
The obligations under the F Gas Regulations include leak testing, recovery of refrigerant, record keeping for equipment containing 3kg of refrigerant and above, recording of training and labelling of new equipment. Insufficient testing per annum is a common failure in this area. Testing frequencies are influenced by the type and amount of refrigerant contained within the system(s) installed. If this is not accounted for when conducting PPM you can unknowingly be non-compliant.
Missing paperwork and certifications in the F Gas log book is another common issue. As a minimum there should be an asset register containing quantity and type of refrigerant for each piece of equipment. Details of any refrigerant added to the system(s), identity of the maintenance provider or personnel who performed the servicing including dates and results of leak tests.
Water Risk Assessment
The Water Risk Assessment document is usually undertaken on behalf of the Landlord by the buildings managing agent. This document should be provided as a hard copy and kept on site. This document will normally include recommendations applicable to the installation which has been surveyed. The recommendations may include removal of pipework dead legs, cleaning and chlorination of cold-water storage tanks (CWST) and advice regarding periodic testing.
A general mistake is that the recommendations have either not been carried out or not correctly documented. Upon completion of the works / maintenance, the recommendation needs to be marked as complete and signed off within the risk assessment document. This is an important document which should be reviewed on a regular basis.
Water Hygiene ACop L8
ACop L8 is designed to prevent the growth of legionella bacteria by ensuring the water systems within buildings are maintained within set parameters. Various checks and tests are required in order to comply with ACop L8. Common failures with regards to these tasks include poor record keeping, inaccuracy of testing especially with regards to water temperature, testing of thermostatic mixer valves (TMV’s), as well as flushing of infrequently used outlets.
Closed Water System
The testing and treatment of closed water systems is essential for the avoidance of microbiological fouling, corrosion and scale which could result in energy inefficiencies, poor performance and the failing of the system or components. System testing is variable but is generally carried out at monthly or quarterly intervals. This frequency tends to be increased on new or modified systems for the first 6 months following completion. Sampling should be generally taken from a full bore drain point and not from locations such as dosing pots. This testing is often not given the importance it deserves and tends to get overlooked or missed. Yet again, the main failure is the recording of accurate results and ensuring that the required inhibitor levels are adjusted according to the results and system type.
Wet / Dry Riser
There is a requirement within BS9990 that a visual inspection should be carried out every 6 months to check for damage or vandalism and verify as far as practicably possible that the systems are in good working order. The annual dry riser test which is a legal requirement should be a wet test incorporating a pressure test and flow test. The PPM audit will check the documentation relating to the dry riser testing and ensure the testing has been carried out as required. Again, documentation is not always provided following testing. In addition, all recommendations should be validated and carried out to ensure the system(s) continue to be fully compliant.
Fire Alarm
The testing of fire alarm systems comprises various levels which include weekly checks which can be carried out by site personnel as well as annual testing and servicing which is required to be undertaken by suitably qualified and competent personnel. The weekly fire alarm test comprises of a bell test which requires the operation of a break glass device using a test key. One issue here is that a different call point should be used each week to verify the correct operation at various locations of the building. The test results are to be recorded within the site log book and should not utilise a separate stand alone record system. The annual testing can be broken down into bi-annual or indeed quarterly visits if required but to comply with BS5839 all devices should be tested at least once annually. Although most sites and contractors comply with this, again, the recording of testing is generally the downfall and it is this element which often requires improvement.
Emergency Lighting
Emergency lighting testing comprises two elements which is carried out monthly and annually. The monthly testing should be of sufficient duration to test the operation of the emergency light fittings and should ensure that all fittings are tested at least once per month. The annual testing should comprise a multi-hour discharge test to ensure the fitting operates for the rated duration ie. 3 hours for a 3-hour rated fitting.
The major failing of maintenance contractors is with regards to the recording of the tests and results. It is essential that in order to ensure all fittings are tested an asset register should be produced and all fittings numbered accordingly. It is also advantageous to produce location drawings to assist engineers during testing. The test certification should indicate the fitting location or ID number, fitting type, result of test and required remedial actions. Once remedial actions have been identified then these should be rectified and on completion signed off as complete on the remedial action list.
Portable Appliance Testing (PAT)
Portable appliance testing is a test which is often overlooked. This test is vitally important to ensure that all portable appliances are serviceable for use and includes anything that may be plugged into a power supply and be moved. Where portable appliance testing is carried out, various companies make the mistake of only providing ‘Pass’ or ‘Fail’ stickers affixed to the plug, flex or appliance. However, this not acceptable, and a full certificate should be provided indicating the test results of all appliances. The frequency of testing is variable but in an office environment this would be done annually.
TM44 Air Conditioning Inspection
There is a legal requirement to carry out an inspection of all air conditioning systems with a cooling capacity of 12kW and over. This is a requirement which requires action by the building owner or managing agent, and often gets overlook. This inspection can only be carried out by suitably qualified and accredited personnel. The inspection not only looks at the heating and ventilation plant but the whole infrastructure within the building as well as the construction and design of the building. Once complete, the certificate and accompanying report has to be lodged on the Governments web portal operated by Landmark (only for England & Wales) where it remains valid for a period of 5 years. The report which is produced will highlight various recommendations and energy saving opportunities. As such should be reviewed and appropriate initiatives carried out to reduce energy consumption and/or improve environmental conditions within the building.
5 Year Fixed Wiring Testing
Generally, the 5-year fixed wiring testing is undertaken within the required time-frame but quite often there are issues raised within the certification. These are listed as C1, C2 & C3 faults where C1 is the most serious and requires immediate action whether this is rectification or isolation. The C2 and C3 faults are the ones which are generally overlooked and left untouched. All C2 faults should be investigated and a quotation raised in order that the works can be approved for actioning. Although the C3 faults do not have to be rectified it is recommended that they are also included. Once complete a certificate should be produced and issued to confirm that the works have indeed been completed, and that the installation is fully compliant. These certificates should be filed within the onsite log book in order that it may be inspected as required.
In conclusion, the number one issue is paperwork. This is not just the filing of certification but the recording of test results by onsite engineers. In addition, poorly completed engineers’ worksheets prevent audits to be undertaken accurately. Providing detailed paperwork would enable potential issues i.e. regular plant faults to be highlighted and investigated as part of the PPM audit and as such assist in the production of capital expenditure (CAPEX) forecasts. PPM auditing is not to be viewed as a finger pointing exercise but as a necessary requirement to ensure the buildings occupants, building management and Landlords are kept safe and free from illegal situations which could be inspected by various authorities at any time as they are at liberty to do.
Steve Shires, Associate Director
Steve joined ETS in 2015 and acts as our Account Manager for a number of our large blue-chip clients. Drawing on his broad range of experience, he is fully operational in the field, undertaking surveys, audits, Project Management and providing technical expertise / support.
Final thoughts
If you are looking for an energy management system that is tailored to your business needs, ETS can provide you with 25 years of experience in dramatically improving energy efficiency and reducing environmental impacts. Whether your businesses have individual assets or large international portfolios, ETS can assist you in saving substantial amounts of money while significantly reducing your carbon performance.
To discuss your requirements, get in touch. You can contact us by calling 0117 205 0542 or drop us an email at enquiries@energy-ts.com.
What is a PPM Audit?
Planned preventative maintenance (PPM) is designed to ensure that plant and equipment is regularly maintained in line with manufacturers recommendations. The purpose of PPM is to reduce reactive maintenance and prolong plant life expectancy.
PPM audits ensure that the incumbent contractors responsible for maintaining sites are carrying out their duties as per contract. A PPM Audit will also check that the maintenance provider is adhering to SFG20 standards, assuming this was an inclusion within the contract. In addition, a PPM audit will also review and comment on conformance items such as water hygiene, F Gas, electrical testing etc. which require completion in order to maintain legal compliance.
Our consultants carry out regular PPM Audits on behalf of our clients. Associate Director, Steve Shires discusses the top 10 non-conformance issues uncovered when conducting PPM audits.
F Gas
The obligations under the F Gas Regulations include leak testing, recovery of refrigerant, record keeping for equipment containing 3kg of refrigerant and above, recording of training and labelling of new equipment. Insufficient testing per annum is a common failure in this area. Testing frequencies are influenced by the type and amount of refrigerant contained within the system(s) installed. If this is not accounted for when conducting PPM you can unknowingly be non-compliant.
Missing paperwork and certifications in the F Gas log book is another common issue. As a minimum there should be an asset register containing quantity and type of refrigerant for each piece of equipment. Details of any refrigerant added to the system(s), identity of the maintenance provider or personnel who performed the servicing including dates and results of leak tests.
Water Risk Assessment
The Water Risk Assessment document is usually undertaken on behalf of the Landlord by the buildings managing agent. This document should be provided as a hard copy and kept on site. This document will normally include recommendations applicable to the installation which has been surveyed. The recommendations may include removal of pipework dead legs, cleaning and chlorination of cold-water storage tanks (CWST) and advice regarding periodic testing.
A general mistake is that the recommendations have either not been carried out or not correctly documented. Upon completion of the works / maintenance, the recommendation needs to be marked as complete and signed off within the risk assessment document. This is an important document which should be reviewed on a regular basis.
Water Hygiene ACop L8
ACop L8 is designed to prevent the growth of legionella bacteria by ensuring the water systems within buildings are maintained within set parameters. Various checks and tests are required in order to comply with ACop L8. Common failures with regards to these tasks include poor record keeping, inaccuracy of testing especially with regards to water temperature, testing of thermostatic mixer valves (TMV’s), as well as flushing of infrequently used outlets.
Closed Water System
The testing and treatment of closed water systems is essential for the avoidance of microbiological fouling, corrosion and scale which could result in energy inefficiencies, poor performance and the failing of the system or components. System testing is variable but is generally carried out at monthly or quarterly intervals. This frequency tends to be increased on new or modified systems for the first 6 months following completion. Sampling should be generally taken from a full bore drain point and not from locations such as dosing pots. This testing is often not given the importance it deserves and tends to get overlooked or missed. Yet again, the main failure is the recording of accurate results and ensuring that the required inhibitor levels are adjusted according to the results and system type.
Wet / Dry Riser
There is a requirement within BS9990 that a visual inspection should be carried out every 6 months to check for damage or vandalism and verify as far as practicably possible that the systems are in good working order. The annual dry riser test which is a legal requirement should be a wet test incorporating a pressure test and flow test. The PPM audit will check the documentation relating to the dry riser testing and ensure the testing has been carried out as required. Again, documentation is not always provided following testing. In addition, all recommendations should be validated and carried out to ensure the system(s) continue to be fully compliant.
Fire Alarm
The testing of fire alarm systems comprises various levels which include weekly checks which can be carried out by site personnel as well as annual testing and servicing which is required to be undertaken by suitably qualified and competent personnel. The weekly fire alarm test comprises of a bell test which requires the operation of a break glass device using a test key. One issue here is that a different call point should be used each week to verify the correct operation at various locations of the building. The test results are to be recorded within the site log book and should not utilise a separate stand alone record system. The annual testing can be broken down into bi-annual or indeed quarterly visits if required but to comply with BS5839 all devices should be tested at least once annually. Although most sites and contractors comply with this, again, the recording of testing is generally the downfall and it is this element which often requires improvement.
Emergency Lighting
Emergency lighting testing comprises two elements which is carried out monthly and annually. The monthly testing should be of sufficient duration to test the operation of the emergency light fittings and should ensure that all fittings are tested at least once per month. The annual testing should comprise a multi-hour discharge test to ensure the fitting operates for the rated duration ie. 3 hours for a 3-hour rated fitting.
The major failing of maintenance contractors is with regards to the recording of the tests and results. It is essential that in order to ensure all fittings are tested an asset register should be produced and all fittings numbered accordingly. It is also advantageous to produce location drawings to assist engineers during testing. The test certification should indicate the fitting location or ID number, fitting type, result of test and required remedial actions. Once remedial actions have been identified then these should be rectified and on completion signed off as complete on the remedial action list.
Portable Appliance Testing (PAT)
Portable appliance testing is a test which is often overlooked. This test is vitally important to ensure that all portable appliances are serviceable for use and includes anything that may be plugged into a power supply and be moved. Where portable appliance testing is carried out, various companies make the mistake of only providing ‘Pass’ or ‘Fail’ stickers affixed to the plug, flex or appliance. However, this not acceptable, and a full certificate should be provided indicating the test results of all appliances. The frequency of testing is variable but in an office environment this would be done annually.
TM44 Air Conditioning Inspection
There is a legal requirement to carry out an inspection of all air conditioning systems with a cooling capacity of 12kW and over. This is a requirement which requires action by the building owner or managing agent, and often gets overlook. This inspection can only be carried out by suitably qualified and accredited personnel. The inspection not only looks at the heating and ventilation plant but the whole infrastructure within the building as well as the construction and design of the building. Once complete, the certificate and accompanying report has to be lodged on the Governments web portal operated by Landmark (only for England & Wales) where it remains valid for a period of 5 years. The report which is produced will highlight various recommendations and energy saving opportunities. As such should be reviewed and appropriate initiatives carried out to reduce energy consumption and/or improve environmental conditions within the building.
5 Year Fixed Wiring Testing
Generally, the 5-year fixed wiring testing is undertaken within the required time-frame but quite often there are issues raised within the certification. These are listed as C1, C2 & C3 faults where C1 is the most serious and requires immediate action whether this is rectification or isolation. The C2 and C3 faults are the ones which are generally overlooked and left untouched. All C2 faults should be investigated and a quotation raised in order that the works can be approved for actioning. Although the C3 faults do not have to be rectified it is recommended that they are also included. Once complete a certificate should be produced and issued to confirm that the works have indeed been completed, and that the installation is fully compliant. These certificates should be filed within the onsite log book in order that it may be inspected as required.
In conclusion, the number one issue is paperwork. This is not just the filing of certification but the recording of test results by onsite engineers. In addition, poorly completed engineers’ worksheets prevent audits to be undertaken accurately. Providing detailed paperwork would enable potential issues i.e. regular plant faults to be highlighted and investigated as part of the PPM audit and as such assist in the production of capital expenditure (CAPEX) forecasts. PPM auditing is not to be viewed as a finger pointing exercise but as a necessary requirement to ensure the buildings occupants, building management and Landlords are kept safe and free from illegal situations which could be inspected by various authorities at any time as they are at liberty to do.
Steve Shires, Associate Director
Steve joined ETS in 2015 and acts as our Account Manager for a number of our large blue-chip clients. Drawing on his broad range of experience, he is fully operational in the field, undertaking surveys, audits, Project Management and providing technical expertise / support.
Related Article
8 Ways Businesses Can Reduce Energy Use in the Workplace This Winter
Discover how to comply with ESOS Phase 4 and unlock energy-saving opportunities for your business. This guide explains the requirements, highlights key deadlines, and provides actionable strategies. Learn how energy audits, tailored action plans, and expert support can reduce costs, improve efficiency, and align your organisation with sustainability goals.
ESOS Action Planning: Complying with Phase 4 and Implementing Energy Saving Strategies
Discover how to comply with ESOS Phase 4 and unlock energy-saving opportunities for your business. This guide explains the requirements, highlights key deadlines, and provides actionable strategies. Learn how energy audits, tailored action plans, and expert support can reduce costs, improve efficiency, and align your organisation with sustainability goals.
Important Update: What You Need to Know about ESOS Phase 3
Time is ticking for the ESOS Phase 3 deadline. The Environment Agency announced that the reporting system is available now. For organisations qualifying for ESOS Phase 3, the deadline for submitting a compliance notification is 5 June 2024, and organisations should still look to meet this compliance notification deadline where possible.