THIS ARTICLE AT A GLANCE
CONTACT ETS
If you have any questions or would like to discuss further what you should be doing, ETS is here and willing to help.
Call 0117 205 0542
Email enquiries@energy-ts.com
Submit a contact form
CHECK OUR SERVICES
The Importance of Planned Preventive Maintenance (PPM) Audits
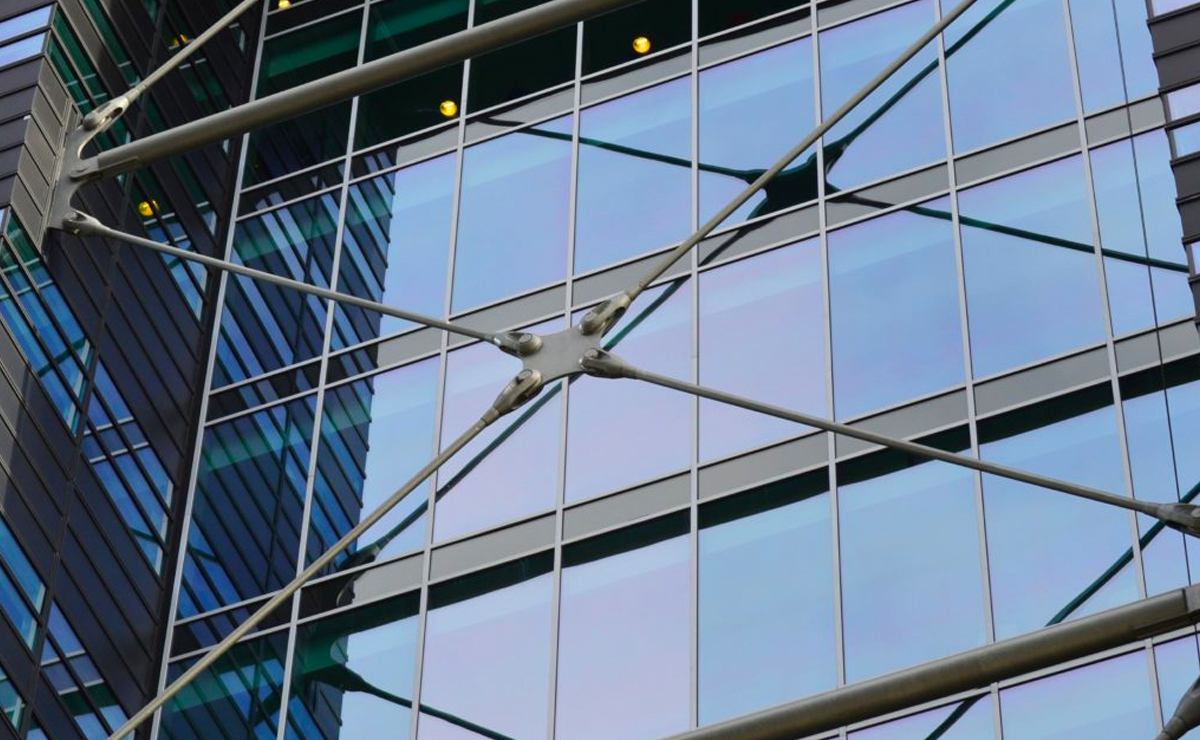
It is well known that buildings tend to not operate as intended which can often cause performance gaps with energy and operational efficiency. Through careful management of an organisation’s assets and utilities (buildings, plant and equipment), businesses can further enhance their profitability. For an owner / occupier, this is critical to not only optimise building energy and environmental performance, but to also manage cash-flow in the case of plant failure which can often carry a significant cost burden.
Why is Planned Preventative Maintenance important?
Some of the most common factors that affect operational efficiency can be addressed by carrying out regular maintenance. Planned Preventative Maintenance (PPM) is essential to ensure that buildings not only operate at optimum efficiency but also adhere to statutory requirements. It also helps to extend the life span of equipment and prevent degradation and failure.
Why undertake Planned Preventative Maintenance Audits?
A PPM programme should prevent a building from experiencing unexpected plant failure and mitigate compliance risks. However, you should not solely depend on your maintenance provider to alert you of potential issues. You should still review the quality of the maintenance undertaken, ensure compliance checks are being carried out regularly, and verify that plant and equipment is operating efficiently.
Building owners and managers often can change regularly, and as a result asset information can often be out-of-date or maintenance records incomplete. Building owners / occupiers may be unaware of the potential issues that may arise unexpectedly from inefficient and poorly maintained equipment. Phil Warren, Managing Director for ETS explains this in more detail here.
Conducting a PPM audit will highlight any potential issues with your current maintenance schedule. It will not only provide insight into the quality of service received from the maintenance contractor but also if works are being carried out to avoid equipment failure. Most importantly, a PPM audit will highlight if plant equipment is being maintained to legal conformance standards as well as highlighting the condition and remaining life expectancy of the systems.
What are the consequences of not undertaking a PPM Audit?
A PPM audit will encompass a review of the scheduling, frequency, compliance and conformance to specification of the PPM services being undertaken by maintenance contractors as well as identifying persistent service failure and faults. It will also provide a life cycle analysis of equipment and a dilapidations report which is important information to help building managers to budget for potential repairs or replacements.
One of the most common issues with PPM is remedial works or tasks not being undertaken, or that evidence of works is not available and not documented correctly. It is important to use an impartial adviser that will be able to review the maintenance regime at your site. If you do not have someone within your organisation with the engineering expertise to undertake a PPM audit, speak to one of our consultants today on 0117 379 0850 or email us at enquiries@energy-ts.com.
More Answers
Final thoughts
If you are looking for an energy management system that is tailored to your business needs, ETS can provide you with 25 years of experience in dramatically improving energy efficiency and reducing environmental impacts. Whether your businesses have individual assets or large international portfolios, ETS can assist you in saving substantial amounts of money while significantly reducing your carbon performance.
To discuss your requirements, get in touch. You can contact us by calling 0117 205 0542 or drop us an email at enquiries@energy-ts.com.